60 Years of Photoresist Materials Part 2: Kodak Thin Film Resist (KTFR)
- Qingzhou Cui
- Feb 13, 2018
- 3 min read
Updated: Mar 29, 2020
The first generation commercial photoresist was made by Kodak and branded as “Kodak Thin Film Resist (KTFR)”. It had been the workhorse for semiconductor industry from 1957 to 1972. The last year of 2017 marked 60-year anniversary for this first photoresist since its initial commercialization.
When William Shockley and his colleagues from Bell labs set out to make first integrated circuit (IC), they first tested dichromated gelatin as photoresist, a well-known imaging material at the time, which was developed by William Henry Fox Talbot (British Patent No 565, 1852). The dichromated gelation worked very well for its resolution, but it didn’t serve its purpose during later silicon dioxide etching, a critical step for IC fabrication. So the team at Bell labs turned to Eastman Kodak for help. Kodak tested an existed material poly(vinylcinnamate) for the request of Bell’s labs. The new photoresist solved the etching issue and seemed to be a great material for IC process of semiconductor industry. However, adhesion issue, later identified by customers during production, failed the poly(vinylcinnamate) for the chance to be the first generation photoresist.
It was very clear at Kodak that a new material route was needed for the semiconductor industry. Martin Hepher, then the head for the Graphic Arts Department at Kodak, suggested to use photo-sensitive rubber to make the new photoresist. He discussed his idea with his lunch partner, Hans Wagner, who then came up with an idea to use bisazide as photo-active compounds to crosslink rubber material. The basic components for the KTFR were born. The ground-breaking KTFR material gained an immediate commercial success and carried the new semiconductor industry over for the next 15 years.
In the original form of the KTFR resist, a synthetic rubber was treated with acidic agent to reduce the degree of unsaturation. It was a partially polymerized material known as B-stage material. The partial polymerization also stabilizes the rubber against O2 mediated cross-linking. In addition, material viscosity and film thickness could be adjusted/controlled from the B-staged material platform. For the commercial version of KTFR, the rubber component from the original formulation was replaced by cyclized poly(cis-isoprene). With the new cyclized poly(cis-isoprene), the precursor molecular weight can be finely tuned and better controlled to achieve proper viscosity and coating thickness. The molecular weight of 150,000 had been used, from which high solid content was maintained to obtain desired film thickness.
The bisazide compound decomposes to form nitrene (Figure 1), which then crosslinks cyclized poly(cis-isoprene) (Figure 2). The nitrene could be quenched by oxygen from surrounding environment. Therefore, a nitrogen blanket is usually needed to prevent O2 from getting to the film.
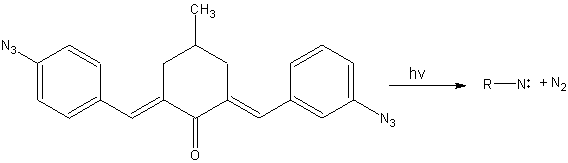
Figure 1. Photodecomposition to form Nitrene from Photo-active Compounds (PAC) of aromatic bisazide.

Figure 2. Nitrene crosslinks cyclized poly(cis-isoprene) for film forming.
The KTFR is negative-tone photoresist. It could work as g-line, i-line, or broad band photoresist (absorption shown Figure 3). It is non-chemical amplified and suitable for solvent development.

Figure 3. Absorption of photo active compound for KTFR.
The KTFR resist had been the major photo-imaging material till 1972. At the time, the desired resolution from semiconductor industry was close to 2um, which is the limit for the KTFR material. The material swelling during development makes it particularly challenging to get smaller features from KTFR. The industry then turned attention to the next generation Novolak/DNQ photoresist. However, even nowadays, some KTFR resists are still in use for some low-resolution applications. Many commercial products are commercially available from different material suppliers.